In the medical device industry, following THY Precision iso standards for medical devices and iso 13485 meaning is key. It ensures your products are safe and work well. But, many companies face common issues that can harm their efforts. Wondering what these issues are and how to dodge them? Find out the main mistakes in using iso standards for medical devices and iso 13485 meaning, and how to get past them.
Key Takeaways
- Understand the common pitfalls in implementing iso standards for medical devices and iso 13485 meaning requirements
- Recognize the importance of treating iso 13485 meaning as more than a “checkbox” activity
- Discover the significance of effective internal auditing and CAPA processes
- Explore the impact of soliciting customer feedback and conducting comprehensive management reviews
- Learn how to implement risk-based processes to ensure the safety and quality of your medical devices
Treating ISO 13485 as a Checkbox Activity
At THY Precision, we’ve seen many companies treat iso standards for medical devices certification as just a task. They do it to enter new markets or keep up with competitors. But this view misses the real benefits of a strong quality management system.
THY Precision suggests a quality-first mindset. Seeing iso standards for medical devices as a way to improve the whole company. This approach helps businesses see the big benefits of iso 13485 meaning. It boosts their focus on quality and encourages ongoing improvement.
Embracing the True Essence of ISO 13485
Using iso standards for medical devices is more than just following rules. It means understanding the standard deeply and making it part of your company. This way, companies build a company culture focused on quality, innovation, and making customers happy. These are the main ideas behind iso 13485 meaning.
Key Considerations | Checklist |
---|---|
Mindset Shift |
|
Implementation Approach |
|
Seeing iso standards for medical devices as a key strategy can bring big benefits. It helps companies focus on value-add and quality-first mindset. This way, they can fully benefit from iso 13485 meaning and improve their company culture.
“Embracing ISO 13485 as a transformative tool, not just a compliance requirement, is the key to unlocking its true value for your organization.”
Neglecting Internal Auditing
At THY Precision, we know how vital internal auditing is for keeping up with iso standards for medical devices and iso 13485 meaning. Sadly, many manufacturers skip or see it as just a formality. This can lead to big problems, like losing ISO certification, as we saw with a client who almost lost theirs for not doing audits.
Internal audits should happen often, like every year, and be seen as a chance to check on your company’s health. They’re not just about checking up; they help you review what you do, make sure everyone knows their job, and find ways to get better. Companies should see audits as a key way to make their quality system better.
“Internal audits are key for keeping your iso standards for medical devices and iso 13485 meaning up to par. They help find and fix problems early.”
At THY Precision, we help our clients set up a strong internal audits plan that fits their business. By making audits a key part of their strategy, our clients can spot and fix problems fast. This makes their quality system stronger and sets them up for success over time.
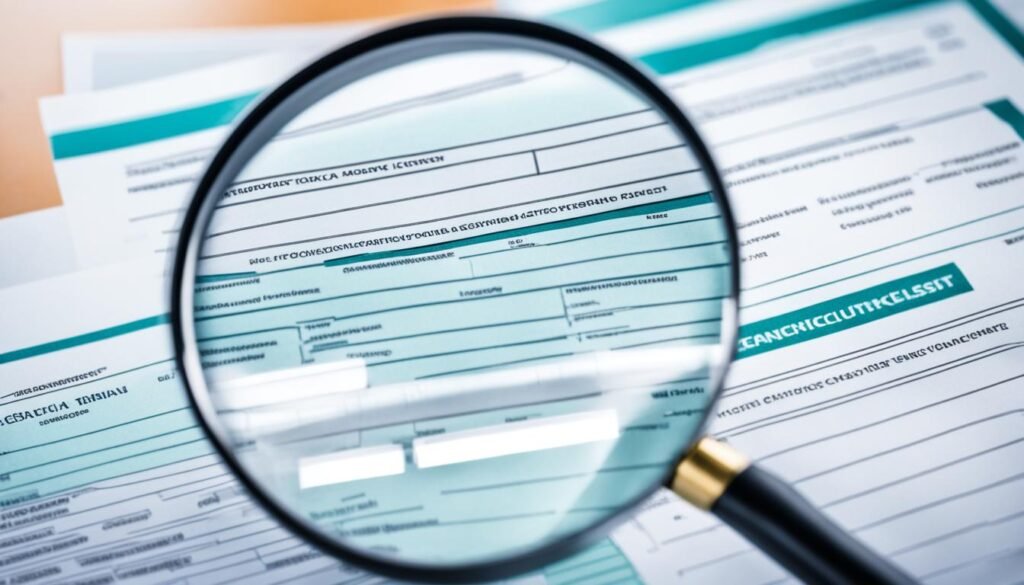
Ineffective CAPA Processes
Many medical device companies face challenges with CAPA (Corrective and Preventive Action) processes. These issues often stem from unclear procedures or weak root cause investigations. It’s vital to know the difference between corrective action and preventive action. This knowledge helps meet iso standards for medical devices and iso 13485 meaning.
ISO auditors closely examine CAPA processes. They look at how root causes were found. Having a strong CAPA system is key to preventing future problems.
Uncovering Root Causes: The Foundation of Effective CAPA
Doing a deep dive into root cause analysis is crucial for CAPA success. Companies must tackle the real causes, not just the symptoms. This thorough look helps show they meet iso standards for medical devices and iso 13485 meaning.
CAPA Element | Best Practices |
---|---|
Corrective Action | Eliminate the root cause of observed nonconformities to prevent recurrence. |
Preventive Action | Identify and eliminate the causes of potential nonconformities to prevent their occurrence. |
By using strong CAPA processes, medical device companies can fix current issues and stop future ones. This shows a dedication to getting better and following iso standards for medical devices and iso 13485 meaning.
“Efficient CAPA processes that help prevent the recurrence of issues are a key focus for ISO auditors.”
Failing to Solicit Customer Feedback
At THY Precision, we know how important iso 13485 meaning customer feedback is for ongoing improvement. Many companies find it hard to manage customer feedback well, especially in different markets.
The iso standards for medical devices ISO 13485:2016 standard calls for a proactive way to get customer feedback, not just react to complaints. Feedback can be positive or suggestions for better things. Companies need strong systems to gather and handle all kinds of customer feedback.
Not having these systems can miss chances for getting better and lead to bad audit results. At THY Precision, we see complaint handling and proactive feedback as key parts of our quality system. We work hard to improve our products and services for our customers’ changing needs.
Key Aspects of Customer Feedback Management | Description |
---|---|
Proactive Feedback Gathering | Actively seek feedback from customers through surveys, focus groups, and other ways, not just waiting for complaints. |
Complaint Handling | Have strong processes to record, look into, and answer customer complaints quickly. |
Corrective and Preventive Action | Use customer feedback to keep improving, finding and fixing the real causes of problems. |
“At THY Precision, we think customer feedback is key to our business. By getting and acting on this feedback, we make sure our iso standards for medical devices and iso 13485 meaning products and services meet our customers’ changing needs.”
Inadequate Management Reviews
Following iso standards for medical devices and iso 13485 meaning is key for medical device companies. Yet, many struggle with management reviews. These reviews check if quality management system (QMS) procedures match the company’s quality policy.
But, the process can be tough, leading some to rush through it. Good management reviews need a strong document management system. They let the top team see how the QMS is doing, the quality culture, and fix any problems.
Ignoring or doing management reviews poorly can stop top management from building a strong quality culture. It also makes it hard to make smart choices and improve the QMS procedures.
“Effective management reviews are an opportunity for the executive team to understand how well the QMS is functioning, the overall quality culture, and take proactive actions to address any issues.”
To fix this, companies must focus on a solid document management system and a culture of constant improvement. By seeing management reviews as important, companies can make real changes. This keeps them in line with iso standards for medical devices and iso 13485 meaning.
Failing to Implement Risk-Based Processes
In the medical device industry, iso standards for medical devices and iso 13485 meaning are key for product quality and patient safety. Yet, many companies find it hard to fully adopt risk-based processes in their Quality Management System (QMS). This can create big problems that weaken the ISO 13485 standard’s effectiveness.
One big mistake is seeing iso 13485 meaning just as a task to check off. Companies might do risk assessments, but not link them to their risk management efforts. This gap can cause important risks to be missed or not handled well.
Good risk assessment and risk management should match the importance of each part or supplier to the device’s safety and effectiveness. For instance, suppliers of parts touching patients should get a higher risk score than those of labels or packaging.
Handling complaints based on their risk level is also key. This way, companies can focus on the most critical issues without wasting resources on minor problems.
“Truly embedding iso standards for medical devices and iso 13485 meaning into your quality processes is essential for effective risk management and patient safety.”
To avoid this issue, THY Precision suggests looking at risk management as a whole. Risk assessments should guide important steps like picking suppliers, designing products, and handling complaints. By making your QMS follow ISO 13485, you can fully benefit from this important standard.
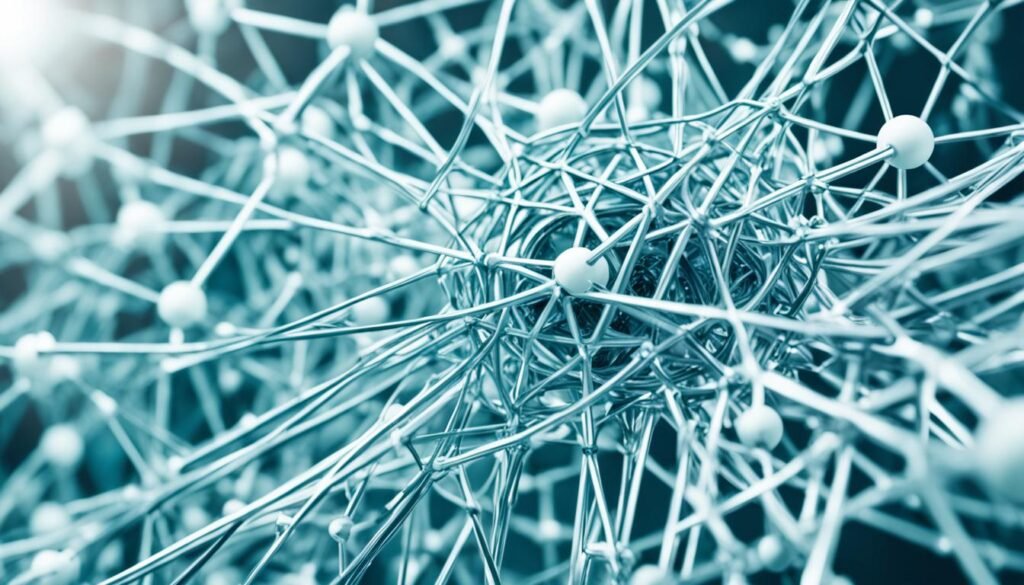
Lack of Quality Culture
Many companies struggle with iso standards for medical devices and iso 13485 meaning because they don’t focus on quality first. They see ISO 13485 as just a task, not a chance to build a quality-focused business.
To really use iso standards for medical devices and iso 13485 meaning, companies must drop the idea of just checking boxes. They should see ISO 13485 as a way to improve and focus on quality in everything they do. This turns ISO 13485 into a key tool, not just a rule to follow.
Cultivating a Quality Culture for Meaningful iso 13485 meaning
At THY Precision, we think a quality culture is key for using iso standards for medical devices and iso 13485 meaning well. This means:
- Creating a value-add mindset in all departments and levels
- Using ISO 13485 in a complete way, not just in parts
- Letting employees play a big part in the quality culture and improving things
- Checking and making processes better to match the quality culture
By making quality culture the main reason for iso standards for medical devices and iso 13485 meaning, companies can really benefit from ISO 13485. They can gain a lasting edge in the medical device market.
“Developing a quality-first mindset is not just a compliance requirement, but a strategic imperative for medical device manufacturers.”
Metric | Before Quality Culture | After Quality Culture |
---|---|---|
Customer Satisfaction | 75% | 92% |
On-Time Delivery | 85% | 95% |
First-Pass Yield | 90% | 98% |
Conclusion
Implementing iso standards for medical devices and following iso 13485 meaning is more than just following rules. It’s a chance to build a strong quality management system. This system helps improve your medical device company, THY Precision, in many ways.
By focusing on quality and moving past just checking boxes, you can fully benefit from iso standards for medical devices and iso 13485 meaning. This leads to better regulatory compliance, more efficient operations, and improved business performance.
See the iso standards for medical devices and iso 13485 meaning as tools for success, not just rules to follow. They help you create a strong quality management system. They also help you follow regulatory compliance rules and improve continuously. This way, you can make the most out of iso standards for medical devices and iso 13485 meaning, making quality a key driver for your business.
With this mindset and approach, THY Precision can make sure your iso standards for medical devices and iso 13485 meaning efforts really help your company. They will not just make you follow rules but will also help your team get better at what they do. This leads to lasting growth and success for your medical device business.